SLS Bearings
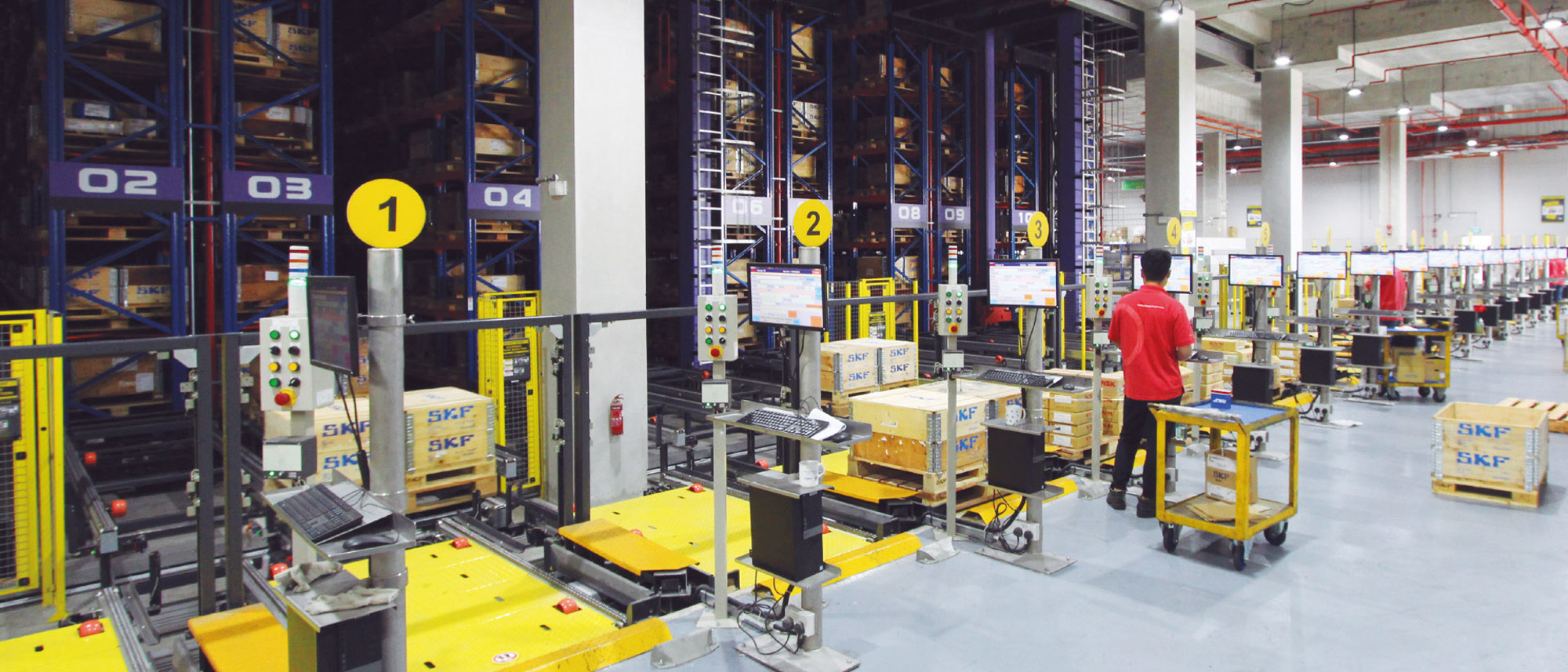
Quick Facts
SLS Bearings is a global product supplier.
Established in 1963, SLS Bearings (Singapore) Pte.Ltd. has always made the most of its location in Singapore, as a thriving hub for intermediate trade. With bearings and transmission parts supplied by manufacturers in Japan, China and Europe, amongst others, it supplies products to auto manufacturers, food producers, and mining companies in Singapore and other countries such as Malaysia, China and Indonesia.
Challenge
Experiencing significant growth and looking to increase their ability to provide immediate dispatch service to their customers, SLS Bearings needed to replace older and smaller AS/RS technology and conventional racking with a modern automated storage and retrieval system. With the information data and material flow of the outdated system, SLS was not able to optimize the operation. Moreover, static rack required the operator to move from aisle to aisle to complete the pick list. Poor ergonomics also reduced the operation efficiency.
Solution
Daifuku installed a new large-scale unitload AS/RS (69'W x 345'L x 88'H) capable of holding up to 19,950 pallets. Stations 1 to 16 on the front side of the AS/RS are used to retrieve products for overseas customers, while stations 17 and 18 are used to store products. Order details can be viewed at a glance on the monitors at each station.
Sortation Transfer Vehicles (STVs) deliver product to the front of the AS/RS where they are loaded, stored, and retrieved for overseas customers, via 18 stations. Products for domestic customers are stored and retrieved from the opposite side. To optimize storage efficiency, partially filled pallets in the system are retreived and consolidated with other partially filled pallets and relocated to the second-floor pick and deposit station.
For fast moving domestic items, in lieu of using a multi-level mezzanine outfitted with conventional rack requiring a high number of pickers, Daifuku installed a high speed, dual fork miniload AS/RS to address their manpower issues. Urgent orders can also be retrieved from a rack side picking station.
Outcome
The new system enabled SLS to store more than twice as many products as previously, within a smaller footprint. By introducing paperless picking, their order picking cycle time was cut 60% and delivery time to customers was cut 20% with near 100% accuracy. The new pick stations reduced injury since items are delivered at an ergonomic level.
The ability to systematically retrieve products in line with shipping schedules has paved the way for standardized operations and significantly improved labor productivity. In short, SLS Bearings has streamline daily operations and productivity has nearly doubled.