Winzer
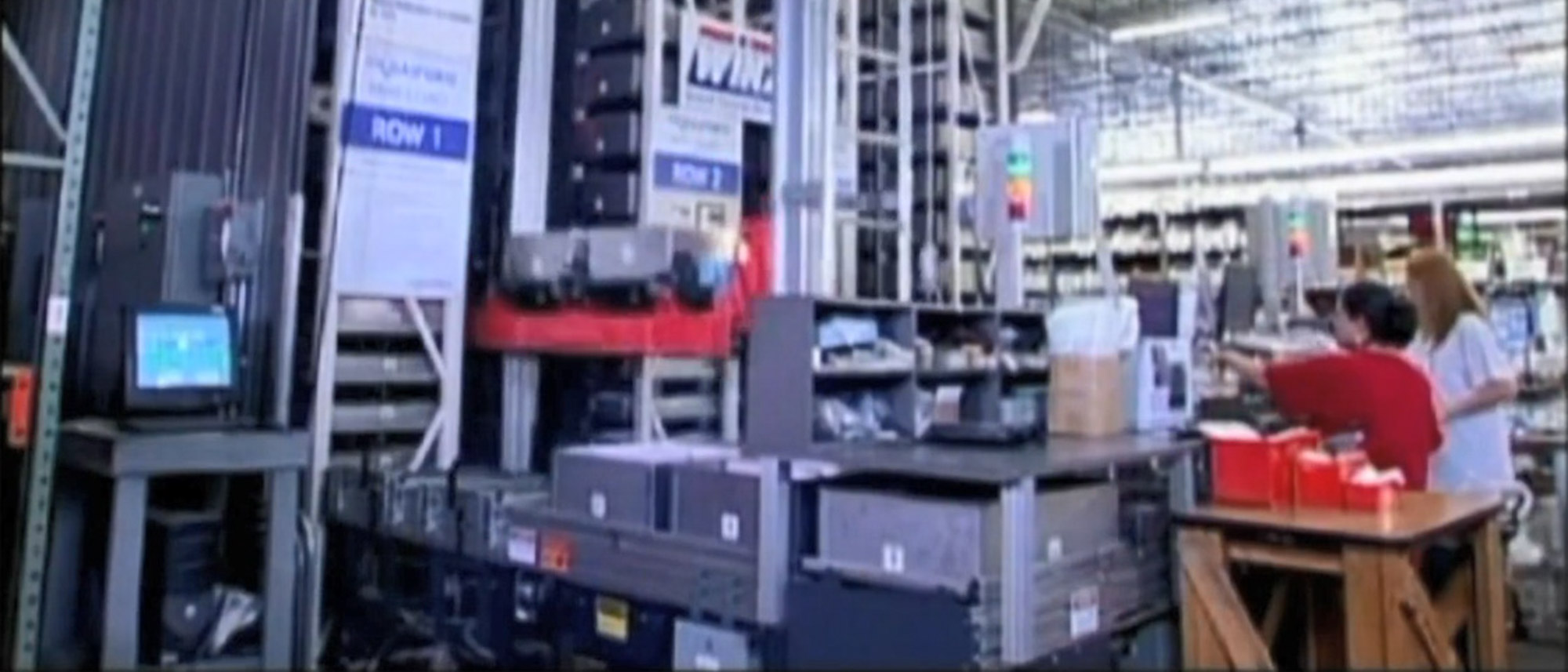
Quick Facts
Winzer has been servicing the Maintenance, Repair, and Operations (MRO) industry since 1978.
Winzer, a GradeEight company, has been servicing the Maintenance, Repair, and Operations (MRO) industry since 1978. With headquarters in the Dallas area, Winzer has over 65,000 in-stock products and access to over 1 million additional high-quality industrial supply products and equipment. Winzer is committed to providing a level of service that is second to none. Featuring a fully automated warehouse system, 99% fill-rate, e-commerce website, extensive customer service, and a network of independently owned franchises, Winzer is your single source supplier for all of your maintenance and repair supplies.
Challenge
To find a quicker way to fulfill and ship orders within 24 hours. Winzer also wanted to avoid moving to a larger facility with more employees by increasing cube efficiency and improving picks-per-hour for each operator.
Solution
Daifuku integrated a new hybrid semi-automated system for their “pick, bag, and tag” operations. By automating a few key areas and adding more error-free picking, Winzer can easily fulfill obligations to the franchisee.
To achieve virtually error-free picking, several systems were put into place to make picking easier and allow error detection before items arrived in the packing area. Six-hundred and sixty Pick-to-Light locations were installed for high demand SKUs. The equipment guarantees virtually 100% accuracy in picking. Also, a two aisle Mini-Load AS/RS was added to automatically pick lower volume items.
Additionally, the entire pick area of shelving and pallet rack was turned into an RF-picking area where picks are scanned with RF guns to ensure accuracy. The installation of these systems guarantees speed and accuracy in the picking process, but Winzer improved in other areas as well. Sixty Put-to-Light consolidation locations were added to ensure that picked products fill the appropriate orders. Automated conveyor moves completed orders to the packing area. The system is highly flexible, so it can maintain efficiency even during peak times.
The entire system is controlled by Daifuku’s warehouse management software (WMS), Warehouse Rx®. Integrated with Winzer’s current host system, the WMS tracks all orders and inventory in real-time. Since items are scanned with RF guns when picked, inventory is automatically updated. The system also tracks the orders which are filled from the mini-Load aisles. Paperless tracking enables order verification while orders are being filled; plus inventory control occurs while data is sent to the host system.
With new equipment and control software in the Dallas distribution center allows Winzer to keep its growth rate in the double digits while fulfilling their promise to hundreds of franchisees around the country. Orders for the company’s 40,000 product inventory are processed within 24 hours of less with lower error rates and higher fulfillment rates.
Outcome
Implementing these systems resulted in shorter travel distances for product and operators, virtually error-free picking, and improved use of space. With a reduction in non-value-added handling, the entire process benefits from fewer touches. Ultimately, Winzer boosted their order handling capacity by 150% while reducing labor cost by 25%.
The new equipment and control software allows Winzer to keep its growth rate in the double digits while fulfilling their promise to hundreds of franchisees around the country with lower error rates and higher fulfillment rates.