How Automated Storage and Retrieval Systems Apply to Manufacturing?
.png)
Automated storage and retrieval systems (AS/RS) has long been synonymous with the material handling industry and has been a part of many distribution centers all over the world. However, AS/RS can also be utilized in a manufacturing environment as well. This article will give insight into AS/RS solutions and how they can be applied to manufacturing environments.
Automated Storage and Retrieval Systems (AS/RSs) Explained
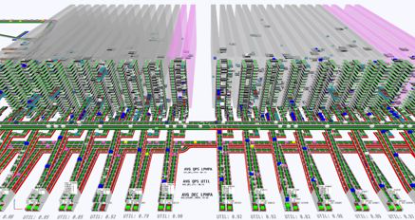
Automated storage and retrieval systems (AS/RSs) are advanced automation technologies that work to store and retrieve items in specific locations around a facility. From unit-load to mini-load types, there are many different varieties of AS/RS systems - and when they're used correctly, they can all help streamline efficiency on the plant floor.
AS/RS systems work using stacker cranes and conveyors to store and retrieve products and goods. Stacker cranes range in size from 5 to 40 meters (16-131 feet) and run vertically, lifting and lowering a carriage section that carries the product load. When it reaches its pre-programmed destination on the AS/RS, it travels into the system bay to either pick up or unload an item or pallet.
AS/RS systems may also utilize a shuttle vehicle to pick and retrieve items. Shuttles tend to utilize a combination of conveyors and lifters and are best used for high-density storage items.
Additionally, it's worth noting that automated warehouse structures can be either free-standing or rack-supported. In a free-standing configuration, the rack is installed separately from the roof and the walls of the building - essentially "free" from any structural support. These tend to be the more common of the two types of structures. A rack-supported building functions as the structural support for a facility's roof and walls and tends to be more common in large manufacturing facilities that need to hold thousands of pallets. Facilities that utilize a rack-supported system are purposefully designed and built to accommodate such.
Some of the key benefits of AS/RS systems include effective use of a facility's space (especially its vertical space), increasing inventory storage density, increasing throughput, minimizing human error and enhancing pick order accuracy, improving safety and worker ergonomics, better product security and reduced labor costs.
Small to Large Scale AS/RS Systems
There are three general types of AS/RS systems - small scale, medium scale and large scale. The one that's best for your manufacturing environment largely depends on how large your operations are and what tasks you need them to do.
Small-Scale
Small-scale systems, for example, are typically installed along the walls of the factory or warehouse to ensure smooth feeding from the storage system to the manufacturing process equipment. Small-scale systems are ideal for storing molds, dies, jigs, raw materials, packaging and more. They tend to have a storage capacity of about 140 pallets and utilize one stacker crane and 3 shuttle carts.
Medium-Scale
Medium-scale AS/RS systems tend to use three stacker cranes and up to six conveyors to help move product, raw materials, parts and more throughout the facility to assist with manufacturing operations. They require more space to function and are ideal for larger facilities. Such systems can typically support up to 1,650 pallets.
Large-Scale
Large-scale AS/RS systems tend to be multi-story operations - and each system floor tends to operate with its own conveyor to help streamline product delivery and retrieval. Large-scale conveyors may have as many as five stacker cranes, can have anywhere from four to 10 conveyors per floor and can support about 3,600 pallets.
Key Benefits of AS/RS Systems in Manufacturing
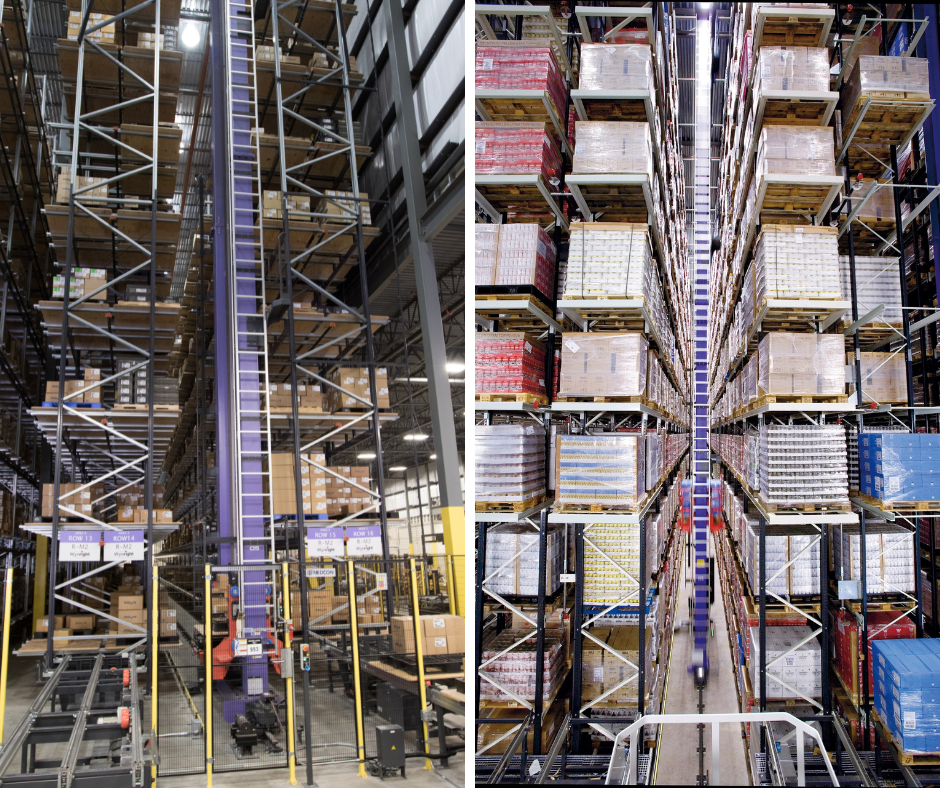
While AS/RS systems are perhaps most commonly associated with warehouse organization and optimization, they also play a key role in manufacturing environments, even though they're not necessarily involved in the manufacturing process. However, the non-manufacturing parts of a facility can play a key role in streamlining operations and enhancing productivity, notably when it comes to intralogistics processes.
The biggest benefit of AS/RS in manufacturing will be using the equipment as a buffer. Some of the key applications of AS/RS systems as a buffer include:
• Helping store and retrieve raw materials
• Supplying and storing parts to assembly lines throughout a facility
• Serving as a work-in-progress buffer
• Storing finished products until it's time to ship
• Storing and retrieving various production tools, like dies and molds
• Aiding with parts storage and order preparation
Time is money on the plant floor. The more efficient things operate, the more products a manufacturing facility is often producing - and the faster it can help get these products to market. Hence, storing and retrieving raw materials, supplying parts to assembly lines, storing finished products, and storing and retrieving production tools all help create a more streamlined and safer manufacturing environment.
By leveraging the high-density storage benefits of an AS/RS you can keep the manufacturing process running even during delays such as downtime, tool change out, or even just natural imbalances on cycle times from one process to another. You can leverage AS/RS storage to hold materials at any point in the manufacturing process to keep the up-stream processes running and keeping the downstream process fed.
Case Study
One specific example, Daifuku was approached by a Radio Manufacturer and Distributer. They had a challenge of feeding raw materials to automated assembly stations. In a traditional environment it took a large amount of manual effort to get the materials to the station. There was also the issue of having the materials ready to be assembled on time in order to keep production running.
This was solved by implementing an AS/RS Solution. By preparing and storing the raw materials in bulk in the AS/RS in advanced of when hey are needed, we are able to deliver the materials just in time to the factory floor when needed. This not only allowed for a more efficient and un-interrupted operation, the client was able to save valuable space on the floor by not having to store the material on the floor.
Contact Daifuku Today
For more information on how AS/RS systems can help enhance productivity in your manufacturing environment, contact Daifuku today.
Daifuku Intralogistics America delivers advanced warehouse automation through high-density AS/RS and robotics, enabling manufacturers to move products more safely, quickly, and efficiently. As a global leader in automated solutions, our mission is to provide innovative systems that elevate your operations to new heights. Contact us today to discover how our AS/RS technology can optimize your manufacturing processes and drive greater efficiency.