Six Steps for Automating Storage in your Distribution Center, Factory or Warehouse.
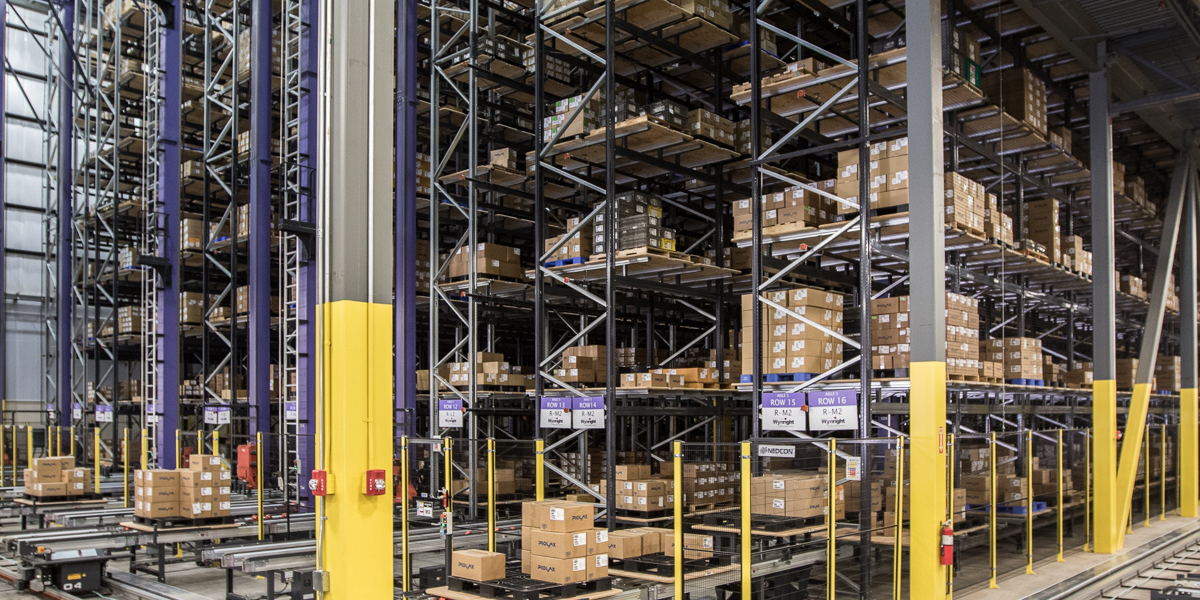
In today's fast-paced manufacturing world, we understand the necessity of a robust, reliable, and optimized storage system. When storing inventory for customers or maintaining spare parts and materials for internal processes, implementing an automated storage and retrieval system (ASRS) can save both time and money.
How does that work? We’ll cover that and more in this quick guide — you’ll learn what ASRS is, how it started, some ways it can help you, and steps to fully automate your storage facility.
What Is ASRS?
ASRS is a technology tailored to automatically place and retrieve loads from defined storage locations. It's typically employed in facilities where there is high inventory movement, and a need for precise, rapid storage and retrieval. The load types can range in size from cases or totes to full pallets. Smaller loads are typically handled utilizing our shuttle and miniload technologies while full pallets are handled with our various unit load ASRS systems.
How ASRS Works?
The Automated Storage and Retrieval System (AS/RS) is essential to a business facility today. An AS/RS comprises storage racks, storage and retrieval equipment, and a Warehouse Management System (WMS) that is a software component. The Birth of Automated Storage / Retrieval Systems (ASRS)
When we talk about ASRS, we can't overlook the role played by Daifuku. As the inventors of the automated storage and retrieval system back in 1966, we sparked a revolution in the world of warehousing and logistics, making high-density pallet storage possible and helping businesses make the most of their available space.
How ASRS Can Help Your Facility
Tobetter understand why an automatic storage facility is desirable, here are somespecific ways that ASRS can help your facility.
Increased Storage Density
ASRStakes advantage of vertical space, allowing you to optimize your floor plan andenhance storage density. By optimizing your current or future building space,your products or parts can be stacked high, freeing up valuable floor space forother critical operations. Land costscan be reduced.
Reduced Labor Costs
ASRSreduces manual labor in the storage and retrieval process, leading tosignificant savings. With this addedautomation,you can focus your efforts on business-critical actions — you don’t have toworry about manually finding, picking, and sorting orders anymore.
Enhanced Accuracy
With ASRS, errors in storage and retrieval are substantially reduced. The automated system accurately tracks where everything is stored, preventing misplaced items, and ensuring the right goods are retrieved every time.
Increased Safety
ASRSeliminates the need for employees to carry heavy loads or use ladders toretrieve items from high shelves, reducing the risk of workplace accidents andpromoting a safer environment for your staff. It also reduces the need for forktrucks to move around your warehouse, reducing the number of accidents.
Improved Inventory Control
ASRSprovides real-time inventory data, making stock management easier. Accurateforecasting and elimination of manual inventory counts lead to operational efficiency.This system can help you understand exactly how much product you have at anygiven time.
Steps to Automate Your Self-Storage Facility with ASRS
Theprocess of automating your storage facility with an ASRS involves several keysteps, from consultation and planning to design, manufacturing, installation,and ongoing support. Here’s a brief overview:
Step 1: Consultation
Theprocess begins with a detailed consultation to understand your specific needs,the type of inventory you handle, the volume of your operations, and yourstorage areas’ physical characteristics. The consultation process also allowsfor a deeper understanding of your current systems, challenges, and goals forthe future.
Step 2: Planning and Engineering
Basedon the consultation, the next step involves careful planning and engineering.The ASRS should be tailored to your specific operations and designed tomaximize efficiency and space usage while reducing labor costs. Planning alsoincludes determining the necessary equipment and technology for your facility.
Step 3: Design
Thedesign phase involves creating a custom layout for your ASRS, taking intoaccount your facility's specific dimensions and unique operational needs. Thegoal is to design a system that integrates seamlessly into your existingoperations.
Step 4: Manufacturing
Oncethe design is finalized, the next step is the actual production of the ASRS.This involves the manufacturing of all required components, such as storageracks, automated storage/retrieval machines, and the controlling software.Quality assurance is a vital part of this phase to ensure reliable performanceof the system.
Step 5: Installation, Commissioning, Start-up, and Training
After manufacturing, the system is then installed in your facility. This includes setting up the physical equipment as well as the installation of the software systems that control the ASRS. Key steps in a successful hand-off to the customer include equipment and controls commissioning, system start-up and testing, as well as training for operations and maintenance.
Step 6: Support
Even after the installation, ongoing support is critical for the smooth functioning of the ASRS. This could include regular system checks, troubleshooting, and maintenance services. Support also involves training, so your staff knows how to use the system effectively.
Why Choose Daifuku's ASRS?
Among the ASRS options available, Daifuku stands out due to our long-standing track record. Our system allows for reliable, high-speed retrieval and storage of items, streamlining your operations. We’ll help you through the full process and provide support after the installation.
The optimization from Daifuku's ASRS systems is due to the advanced methods we use, so you can store items in the most space-efficient way possible. This maximizes the use of available space within your current or future facility, creating more room for your business to grow. It's not just about storage; it's about ensuring your operations run at peak performance.