Unlock the power of project risk management
.png)
Risk is anything that could threaten a project’s scope, quality, schedule, or cost. If you don’t manage risk, risk will find a way to manage you. Talking about risk can be hard but managing it can be easier than you might think. It is impossible to actively manage every possible risk, but certainly the ones that are highly probable and could have a major impact to your project deserve your attention. Actively managing risk is what the best project managers do.
The PMBOK® Project Management Institute. (2017). A Guide to the project management body of knowledge (PMBOK® guide) (6th ed.) includes ten knowledge areas, of which Risk Management is probably the least utilized in practice, because it can feel pedantic and administrative when project teams are immersed in the throes and intensity of a project. The following story by Brick Rossie, Daifuku Intralogistics Senior Project Manager, illustrates how you can change that experience into a fluid, productive practice for your projects.
Years ago, I was attending a project management symposium and was in the audience of around two hundred PMs when the speaker asked, “how many of you practice formal risk management in your organization?” Two hands went up in that audience, and mine was not among the count.
At the time, I was thinking that I’m clever enough and nimble enough to react quickly to my project issues as they arise, and besides, my few experiences with others leading misguided attempts at risk management had proven to me that it was a waste of time and resources – risk registers with line items such as “the supplier might deliver our equipment late”, dutifully coupled with columns for probability, impacts, and mitigation plans such as “call the supplier weekly” were pretty much useless. Beyond that, bi-weekly meetings to follow up, “yep – they might still deliver the equipment late, but I called them” just wasted more of our collective time.
Fast forward many years, many projects, many foreseeable risks escalating to the level of in-your-face issues, and I have become an evangelist for project risk management. The problem in my past was that I understood the textbook theory of risk management, but not the practical application of that theory. The key for me turned out to be learning to focus on identifying the root cause of a risk. It’s not enough to say, “bad stuff might happen” - you also need to dig into the exact why and how an unfavorable outcome could come to pass, and then turn your attention to dealing with root causes rather than symptoms.
So, let’s revisit that supplier-might-deliver-late risk in a more effective way, beginning with imagining the initial risk management meeting of the project team:
Recognizing Risks Naturally
Project Team Meeting – Early in the Project
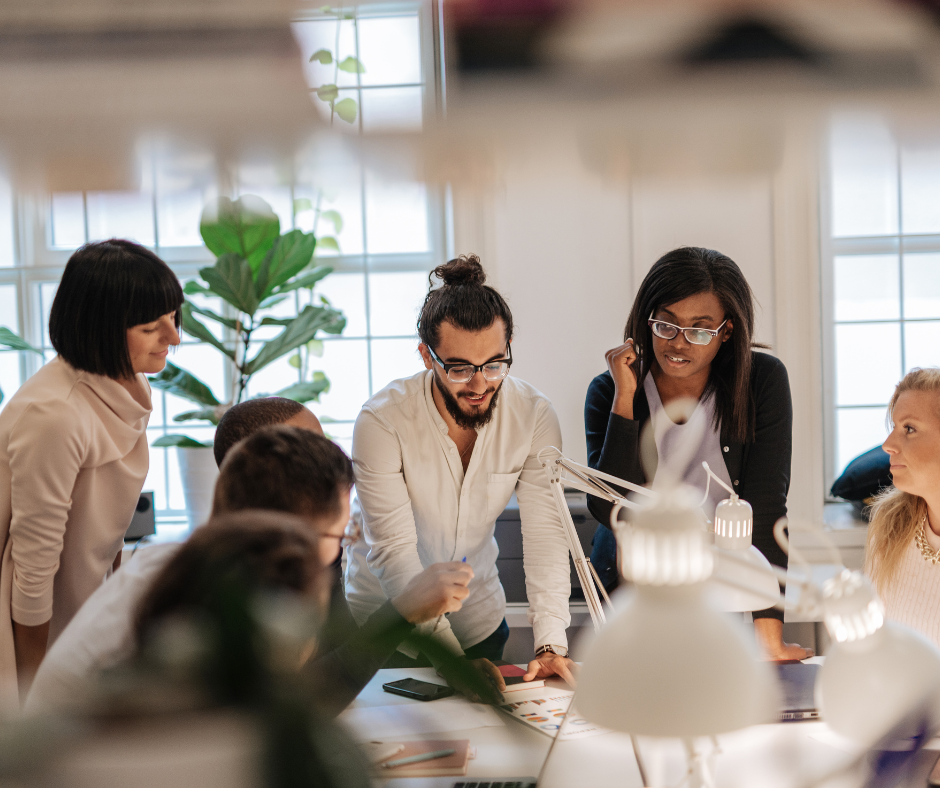
Team member John, commenting about the past week’s activities: We ordered the new amplifiers within our normal lead time, but the supplier has informed me that there is a worldwide shortage of the semiconductor chips needed to build the boxes, and they are not sure that they will be able to get them in time to meet our required delivery date. Without those amplifiers, we will not be able to deploy the new equipment and we’ll be subject to major penalties from our client!
Project Manager Jane: Hmmm - OK – my PM radar just detected and categorized that comment as a risk – one with high probability and high impact – that’s something we need to address. What can be done to make sure that we get enough chips to fulfill that order?
John: Well, we do have ample stock of the older version of the chips in our spare parts inventory – those chips could still meet our base requirements for the project, but the amplifier design will have to be adjusted to accommodate them. I wonder if we can make those available to the supplier for use in the amplifiers?
Jane: Good idea – that might be a reasonable mitigation to ensure that we get the amplifiers on time. I will record this risk in our risk register so that we don’t lose sight of it.
Take Steps to Mitigate a Risk
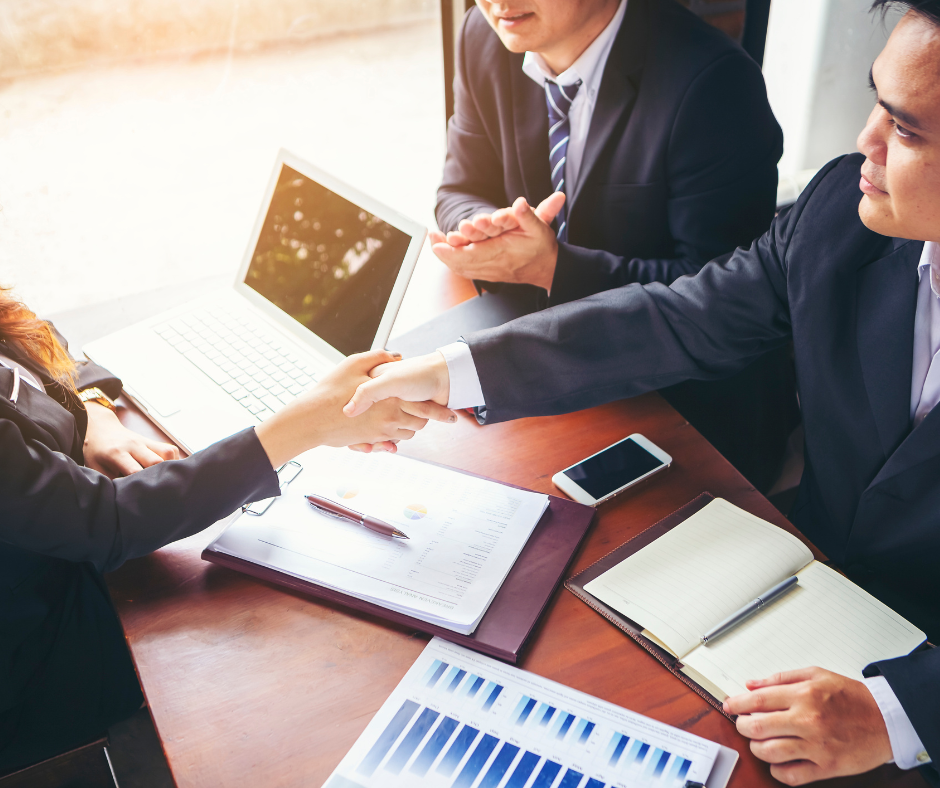
John, take two action items please - call the supplier this week and find out what it would take for them to adjust for the older chip version and still meet the delivery date for the amplifiers. Secondly, call our parts room this afternoon and have them set aside enough chips for us in case we need them. We’ll meet again next week and reassess that risk. OK team - Next item?
Project Team Meeting – The Following Week
Jane: Following up on action items from last week – John, you have two action items - report?
John: The supplier told me that they can make the adjustment for the older chips with no additional charge, but they will need to have the final decision and have the chips delivered no later than sixty days from now. They are still hoping to get the new chips though, which is preferable both for us and them. As for our stock of spare parts, Ted in the parts room pulled a quantity of chips from the shelf and earmarked them for our project. I promised to follow up with him within fifty days, either to send them to the supplier or put them back into inventory.
Moving on to Other Project Tasks
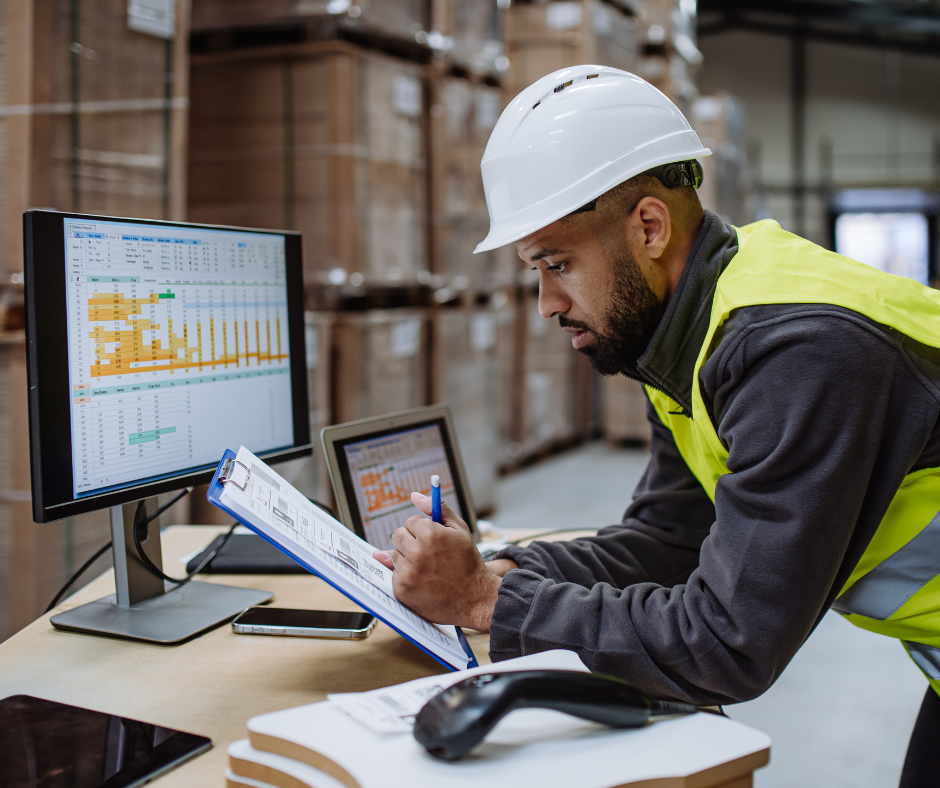
Jane: Great! It sounds like we’ll be able to get our amplifiers on time one way or the other. We’ll leave that risk open on the risk register and reduce the probability of it becoming an issue to “low.” And I’ll add an action item to remind us to follow up with both the supplier and the parts room fifty days from now. Let’s move on to the next item…
Risk Management In a Nutshell…
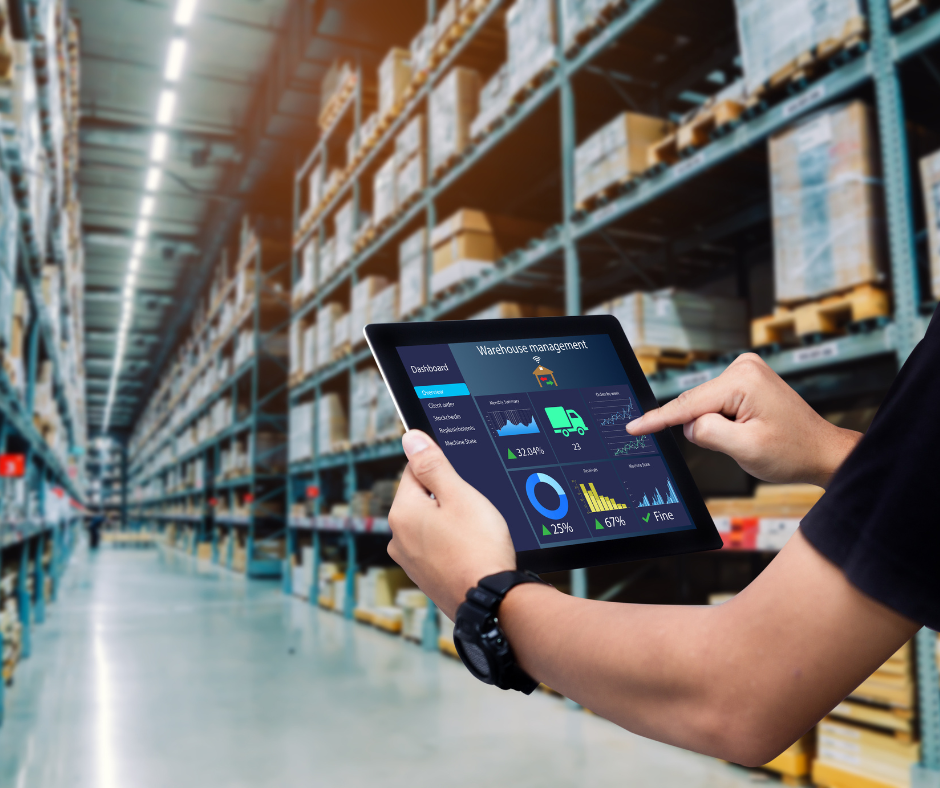
This example illustrates both how project risk management is supposed to work and how simple it can be:
1. John recognized a potential problem and called it out during a routine team meeting. Further, he gave a specific reason for the risk – the scarce supply of semiconductor chips. Jane categorized the problem as a risk and reached into her project management toolbox to address it.
2. Between them, Jane and John assessed that the risk was both high probability and would have high impact to their project success if it came to pass. That combination made working to mitigate the risk a priority, so they came up with a plan.
3. Jane assigned action items designed to mitigate the risk. Following her proven PM skills, she made the actions specific, assigned them to John, and included an expectation for when to complete the items.
4. Continuing with her proven skills, Jane followed up at the next team meeting to make sure the action items were completed. They were of course, and as a result, the probability of the scarce semiconductor risk impacting the project was significantly reduced. Jane nonetheless kept the item open on the risk register and recorded an action item to follow up again fifty days later, at which time the risk item will most likely be further reduced or even closed. In the meantime, the team was able not to worry so much about getting their amplifiers on time, leave their supplier to focus on building amplifiers, and to turn their attentions to other pressing project matters.
This approach to risk management is simple, easily executed and perfectly aligns with Project Management Institute’s® (PMI) recommendations. Once I got myself into the daily habit of recognizing and defining project risks this way, and then managing them with this simple process, my projects magically became smoother and suffered fewer issues. Everyone else probably thought that I was just due for some good luck after all the bumps and bruises in my career, but I believe good risk management probably had more to do with it!
Watch the Webinar On-Demand Here.
Brick Rossie Biography:
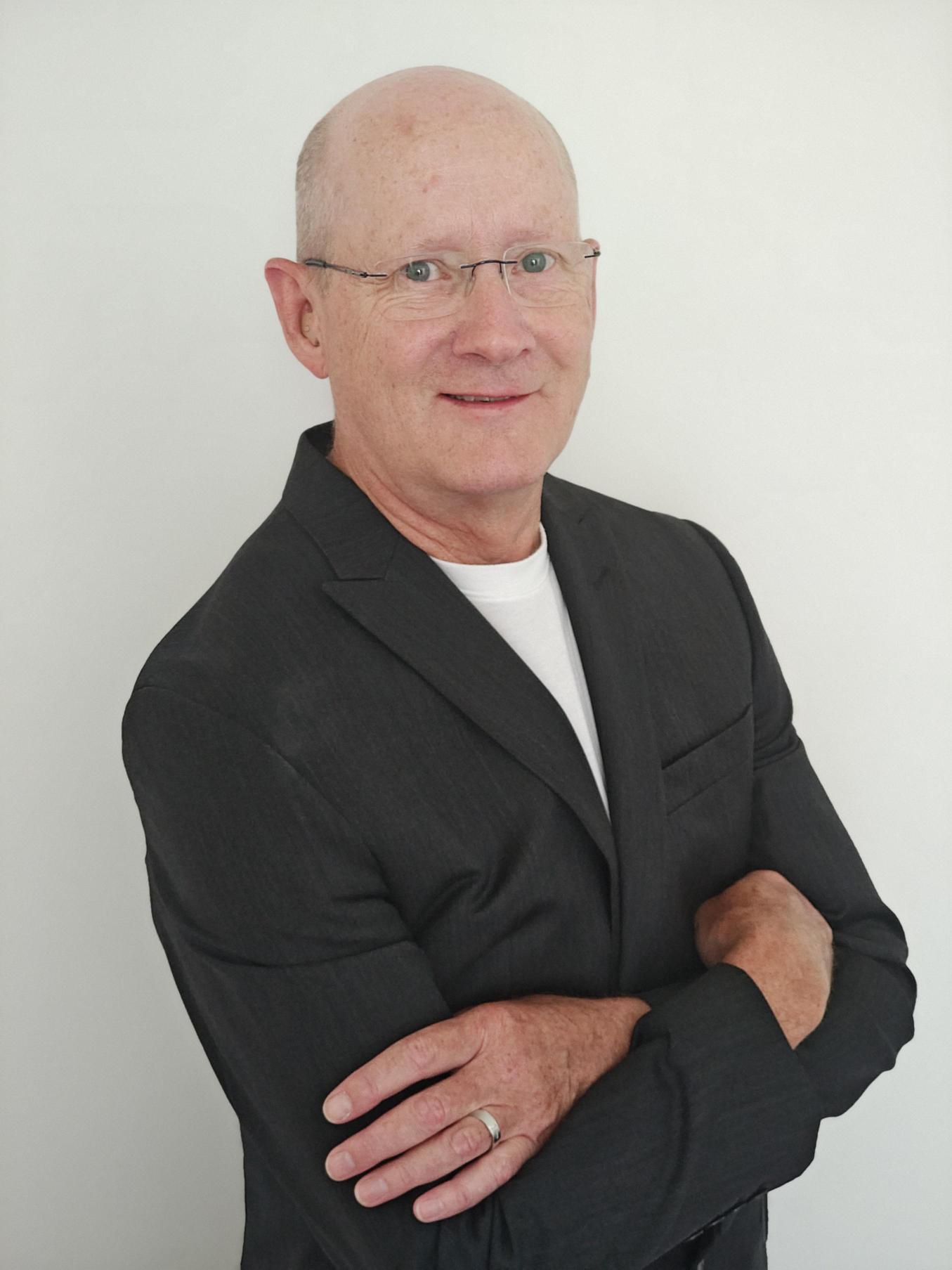
Brick Rossie is a senior manager in the project execution group at Daifuku Intralogistics. With over thirty years of experience, he has managed a variety of projects as both a client and a vendor. His background includes managing enterprise software development projects, capital equipment system installations, plant expansions, and large automated material handling projects. Brick obtained his PMP certification in 2004 and later earned a Master's Degree in Project Management, but believes still that experience is the best (and sometimes the most unforgiving) teacher. His favorite saying is "I'm too lazy to do it the hard way!"
Brick is passionate about helping others develop their project management skills and finding simple solutions to complex problems. In his leisure time, he enjoys sailing on Lake Keowee in South Carolina.
Watch the Webinar On-Demand Here.